News
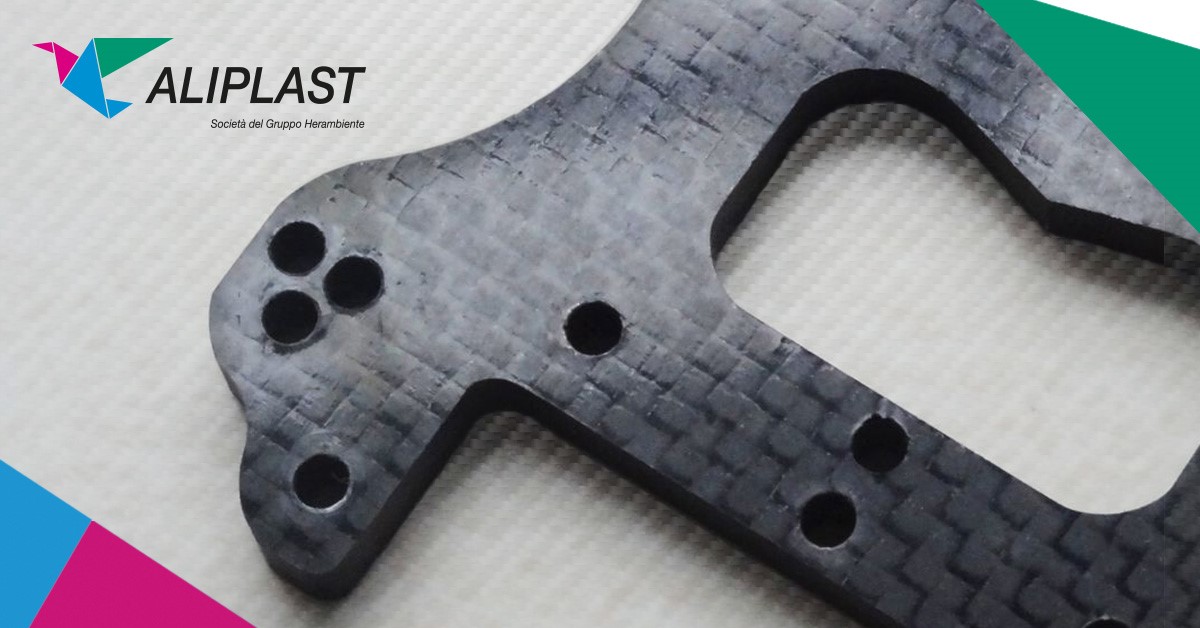
Gruppo Herambiente, CURTI and Università di Bologna partner to recycle carbon fiber
27 February 2023
The Imola plant: a “dispensary” of quality material
One of the most innovative projects in Europe in the recycling field is underway. In the first few months of 2023, the construction of the first Italian carbon fiber recycling plant, one of the first in the whole continent, has begun. The plant will be fitted with machines for the treatment of the material provided by Curti S.p.A. and it will consist of two production lines, the first of which will be operational at the end of this year, while the second one will be inaugurated in 2024. All in a very short time, which shows the determination of Gruppo Herambiente in meeting a real market need.
A pilot plant, produced by Curti, is already running in a space owned by the University of Bologna in Faenza (where the Master in Composite Materials is held) and it is believed that the first prototype piece made with recycled fiber, ready for industrial use, will be produced by the summer. The Imola plant will focus heavily on the quality of the material, rather than the quantity. The production capacity for each line is estimated to be about 160 tons.
The production process of recycled carbon fiber
The regenerated material is obtained through a thermal process called pyrogasification, which frees the more heat-resistant carbon fiber from the resin that is added in the molding and forming stages. The resin breaks down and, through gasification, is reused to generate part of the energy needed for the process, for the highest levels of energy recovery. This stage results in a fabric made of carbon filaments. This material then needs to be sent to other companies specialized in the carding and production of non-woven fabric.
Finally, the fabric is treated again with resin to acquire the properties and shapes that allows it to be used by the industrial sector. The world of carbon fiber is extremely varied and the end material produced is just as varied, with types differing in their weight, filament number, quantity and quality of the resin. The material also has a wide variety of uses as carbon fiber parts are used as structural components of planes, ships and cars, but also in biomedical prosthetics or sports equipment.
Same quality, lower environmental impact
The different material types produced by the Herambiente plant will have one thing in common: their quality, which will be equivalent to virgin products in terms of mechanical strength, which is why automotive and aerospace applications are already being developed. The environmental impact, however, is reduced as the average energy required to produce recycled fiber is 90% lower than virgin material. In addition to this, the specific technology solution chosen by Herambiente leads to a 50% reduction in LCA as compared to the usual means of processing and disposing of carbon fiber waste.
The validity and innovation level of the project are such that it has earned 2 million Euros of European funding through the PNRR (National Reform and Resilience Plan). This material will thus expand Aliplast’s portfolio of recycled plastic and packaging products which will now include recycled carbon fiber, for a wider offer to a more diverse range of industries.
news list