News
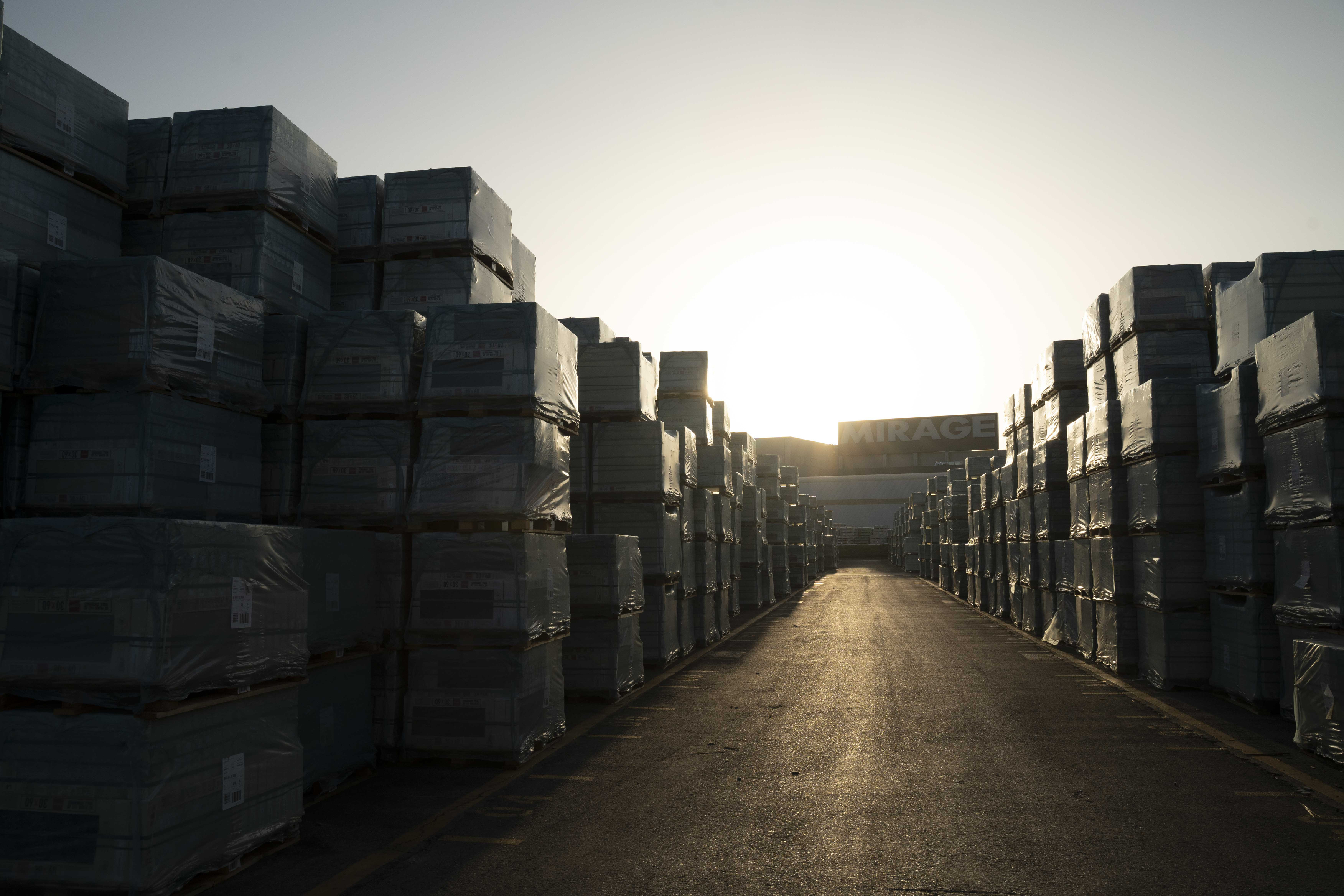
Aliplast and Mirage are partnering to recover plastic waste from the ceramic industry
16 May 2024
Closed Loop for the ceramics industry: how it works
For more than 50 years, Mirage has been producing tiles for interior and exterior wall and floor coverings. The process that leads to their production goes through different steps, during which the tiles are packed several times with the use of plastic films, with a procedure that leads to the use and disposal of large quantities of these films. The recovery project put in place by Aliplast involves, as a first step, a selection and volumetric reduction of this waste material; a phase that takes place directly on site, in the Mirage plants. Then, the material is sent to the Aliplast hub, where it is reconverted into granule and, subsequently, into new packaging film, ready to be fed back into Mirage's production circuit.
The recovery of waste material
The recovery activity is carried out according to a “closed loop” logic, a principle aimed at maximum sustainability that provides for the recovery of plastic waste from companies and the subsequent stages of treatment and regeneration to obtain a quality product, with technical characteristics equal to that made from virgin material, ready to be re-introduced into the production cycle.
The objective value of sustainability
The ceramics industry is increasingly geared toward sustainability. This is why it is important to know precisely to what extent a product or process contributes to the reduction of environmental impact. Quantifying savings objectively has always been one of the cornerstones of Aliplast, which for several years has been monitoring its greenhouse gas emissions associated with its five types of products: PE granule, PE film, PET granule, PET sheet and PET flake. Specifically, Aliplast operates by following the LCA (Life Cycle Assesment) methodology, which assesses the environmental footprint of a product throughout its entire life cycle, so as to obtain an objective survey on its contribution in terms of emissions reduction, including the carbon footprint.
Aliplast's methodology and data
One of the data that is usually measured is CO2 equivalent, based on the IPCC 2013 GWP 100 methodology. The results of this analysis showed that annually, through the production of about 100,000 tons of recycled products, Aliplast avoids the emission of about 170,000 tons of CO2 equivalent (2022 data). This saving corresponds to more than 400,000 barrels of oil. In other words, the contribution of suppliers and customers who choose Aliplast's recycled products has a significant impact in reducing greenhouse gas emissions, comparable to the effect of about 100,000 gasoline-powered cars driving 10,000 kilometers in a year.
The results of the partnership with Mirage
Aliplast supplies more than 500 tons of shrink film to Mirage each year. This is a “Reload” type material, a trademark that identifies Aliplast products that have an extremely high percentage of recycled material, typically more than 80 percent. The use of this type of material results in an environmental benefit of about 1,200 tons of greenhouse gases prevented. In addition, by taking back waste materials from customers, Aliplast avoids their disposal in landfills and gives them a new life with a view to a fully circular economy, with further benefits to the environment.
In conclusion, the virtuous relationship established with Mirage not only results in the supply of a packaging material perfectly suited to the type of use, but also entails real savings for the environment.
news list