News
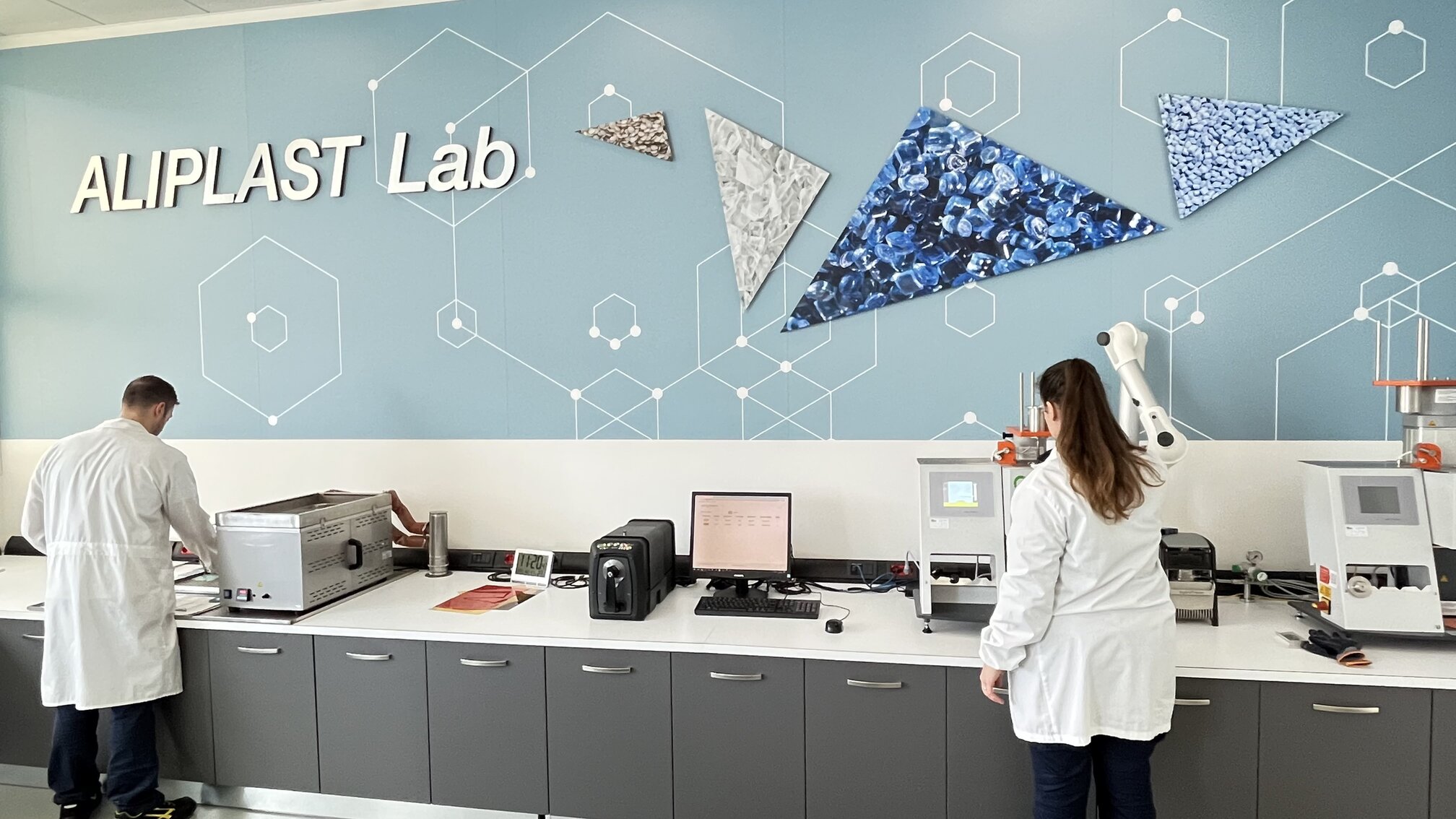
New Aliplast Lab: An open environment of innovation in plastic recycling
23 May 2023
A hub with Italian roots and an international outlook
An open place of innovation to continue moving the frontier of plastic recycling possibilities forward. This is the mission of the new laboratory launched in late April by Aliplast, the European leader in regenerated plastic with more than 100,000 tons of polymer recovered annually, at its headquarters in Ospedaletto d’Istrana, Treviso. The new structure will have Italian roots but a decidedly international outlook, as it will coordinate the analysis, research and development operations of all Italian and European (France, Poland and Spain) production hubs. After all, last year more than a third of the revenue of Aliplast, part of Gruppo Hera, came from abroad.
A lab for innovating together with customers
In addition to the quality analysis of output products (polyethylene and PET granules, sheets, and films), the Lab's activity will focus on the development of new products, also in cooperation with customers. For a company like Aliplast, focused on the high quality of its recycled plastics, this is really the core business. In fact, especially for some supply chains such as cosmetics and food, the development of new products with characteristics and performance that are equal to the virgin material goes through a close partnership with the customer, to study the polymer mixes that can literally shape the desired form, be it packaging or durable good. Typically, customers come to Aliplast with an idea to develop, often presenting a sample of the product they would like to industrialize, and from there the complex work leading to industrialization begins.
A unique structure in Italy to reduce development time and cost
The Aliplast Lab, the only one in the recycled polymer sector in Italy, was conceived precisely as the ideal space for co-design. First, because the new facilities significantly broaden the spectrum of testing and development activities that the company can carry out internally. Secondly, because it is equipped with technologies that can significantly speed up the testing and prototyping times needed to reach mass production, leading to significant cost savings and an improved time to market.
The new laboratory consists of two macro-areas: one for the characterization of raw materials and the analysis of finished products and another for prototyping. The first area is where samples usually arrive from the customers who require a product equal to a virgin one, but with recycled materials. Thus, it is of paramount importance to be able to precisely characterize the product being planned in order to understand what the best recipe of raw materials is to produce it. This area is also where the analysis of finished products to measure their quality and performance takes place. The prototyping area can now rely on a three-layer blown extruder (dedicated specifically to films), a cast line extruder (used for both plate and granule development), and an injection molding machine to transform the produced granule, through a mold, into the predefined sizes. The fields of application are extremely diverse, ranging from charcuterie trays obtained by thermoforming plates, to molding plates to simulate the production of preforms or other containers.
The streamlining of development activities thanks to the new Lab is substantial: generally, within a couple of weeks a new material is studied and characterized, while prototyping is usually set up within another week. It is therefore possible to obtain within a month a so-called machinable product, that is, ready for mass production. The laboratory can also work on multiple projects simultaneously, offering a wide range of applications.
A laboratory to bring industry and universities together
The Aliplast Lab is not only open to customers, but also to partnerships with the academic world. In fact, the company has long collaborated with the universities of Bologna and Padova. These are opportunities that, on the one hand, help the company in carrying out its activities and, on the other hand, help bring the academic and manufacturing worlds, which are too often far apart, closer together. Over the years, this collaboration with universities has also taken the form of the joint management of projects funded by the European Union. One of these involved the development of a 3-layer PET sheet suitable for food contact consisting of 100% recycled PET where the outer layers, consisting of decontaminated R-PET granule, serve as a functional barrier for the middle layer consisting of R-PET flakes derived from mechanical recycling of PET bottles. This structure allowed compliance with current food legislation as well as the optimization of the energy sustainability of available resources.
Guarda il video sull'Aliplast Lab
news list